摩擦、磨损、滑动试验与观察、分析、测量
运动的部件与部件之间会发生摩擦。以传导汽车及电车动力的动力总成为例,会用到离合器、变速器、传动轴等众多部件,这些部件被称为“摩擦部件”。
摩擦部件会在摩擦力的作用下发生发热及磨损。摩擦造成的发热及磨损,是机械系统故障的主要原因,由此导致的经济损失也很大。为了减轻上述损失,通过摩擦试验、磨损试验、滑动试验对相应部件及材料特性进行评估的试验,都属于“摩擦学试验”。
下面我们将围绕摩擦磨损试验、滑动试验,从研究所有摩擦的摩擦学角度出发,对试验及测量方法进行说明,并介绍使用4K数码显微系统的课题解决案例。

摩擦、磨损、滑动试验
让试验片与摩擦材料发生摩擦,测量摩擦系数*及磨损量的试验。
在使用摩擦部件的各行各业,在新产品研究开发、产品品质评估及受托分析中,经常会遇到用摩擦磨损试验及滑动试验评估原材料变化的案例。此类试验在润滑油/润滑脂生产、轴承及滑轮部件供应、电机制造等摩擦部件的关联行业中,属于保障品质的必要试验。
摩擦系数:将摩擦力对接触面造成的影响数值化后的系数。摩擦系数没有单位,用“μ”表示。分为“动摩擦系数”与“静摩擦系数”,具体数值取决于物体性质及表面加工。
摩擦、滑动、磨损试验的方法
摩擦试验和滑动试验一样,都是测量摩擦力大小的试验,通常结果都表示为摩擦系数。而磨损试验测量的则是摩擦导致的状态变化,会根据滑动面的变形、划痕及凹陷得出结果。
摩擦系数的测量方法有很多种,例如用测量仪直接测量摩擦力、测出驱动电机的负载功率后进行换算、利用摩擦振动衰减*趋势推算、根据斜面上静置物体开始滑动的角度计算最大静摩擦力*等等。上述试验中的试验对象,不仅包括摩擦和磨损,还有润滑剂的效果及劣化等。
振动衰减:振动随时间推移逐渐变小的现象。也可称为“衰减振动”。
最大静摩擦力:静止物体处于移动临界状态时产生的摩擦力。相对的,在移动过程中产生的摩擦力,就是“动摩擦力”;轴承内滚珠、滚针等产生的摩擦力则是“滚动摩擦力”。
摩擦学试验
对于以轴承为代表的摩擦部件而言,摩擦阻力是一种巨大的负担,更是一种损失。要减小这种阻力,不仅要用材料力学的理念优化部件的机械特性,更要从润滑油流体力学、研究表面热现象的热力学等观点出发,采取综合全面的措施。
这种对摩擦所造成的影响进行全面考察及评估的研究,被称为“摩擦学”,而对摩擦学特性进行评估的试验,则被称为“摩擦学试验”。
摩擦学试验的必要性
机械装置摩擦导致的发热及磨损会造成材料损失,进而引发机械阻力,这被视为机械装置发生故障的最主要原因。减少并控制这种摩擦与磨损,不光是一项预防故障的技术,更是提高机械装置可靠性及性能,降低经济损失的核心技术。
摩擦学试验的特点
在摩擦磨损试验中,即使使用同样的材料,一旦试验片形状、试验方式、环境条件改变,经常会得到截然不同的特性值。因此,我们必须掌握作为摩擦磨损试验研究对象的实际现象所对应的具体条件,以相近的条件进行试验。此外,润滑材料的物性与界面化学性质也会对润滑剂的性能造成很大的影响。尤其是固体润滑剂*,相较于油和润滑脂,它的耐荷重性能更强,可以被用作油和润滑脂的添加剂。
摩擦学试验需要在接近于实际使用条件的条件下进行,再现摩擦相关的实际环境。评估对象不仅包括摩擦部件所用的原材料,还有润滑剂及基于部件形状的特性等。
固体润滑剂:保护材料表面,减轻摩擦影响,减少摩擦及磨损的固体物质。包括二硫化钼、石墨、PTFE(Poly Tetra Fluoro Ethylene)等。
摩擦试验、磨损试验、滑动试验观察应用案例
摩擦磨损试验的试验片及摩擦部件都采用了立体结构,其中不少还含有强反射面。这种情况下,如果用显微镜进行测量分析,检测人员就必须进行对焦、防反射光等处理,操作难度很高。还存在无法定量化研究等问题。
近年来,随着科技的发展,数码显微系统已经成功解决了诸多课题,大幅改善了摩擦磨损试验的效率。
高效观察具有一定深度的轴承凹陷
对轴承受到打击后产生的凹陷进行观察。观察面非平面时,显微镜高倍率观察会受到细微高度差的影响,无法准确对焦,要耗费大量时间仔细调焦。
4K数码显微系统“VHX系列”则配备了高分辨率HR镜头和电动镜头转换器,无需更换镜头,就能进行20至6000倍的“无缝缩放”,可快速调节到目标倍率。

- A:用数码显微系统进行观察
- B:用显微镜进行观察
- C:近侧面的凹陷观察
- D:远侧面的凹陷观察(500×)
还能利用“导航实时合成”自动进行深度合成,对目标物整体进行全幅对焦。借助这项功能,可以拍摄到远近全程对焦的超高精细4K图像,轻松实现正确高效的放大观察、外观检测及评估。
还能自动识别已连接的镜头,同时管理拍摄的图像和倍率数据。
数码显微系统具有能够在整体图像和局部放大图像之间无缝缩放的高精细放大观察功能,以及优异的数据管理功能,可有效提高检测效率。

用1台设备实现摩擦面损伤的观察及测量
在进行观察和测量时,需要在各个环节换用不同的设备,会耗费大量的时间。
4K数码显微系统“VHX系列”不仅能够清晰地放大观察,还能实现难以进行的各类计算及测量,并获得相应的数值。只需用鼠标简单操作1台设备,就能观察磨损试验后的滑动面剥离*、点蚀*等损伤,实施有助于开展粗糙度检测的平面测量及粗糙度测量。
剥离:材料滚动疲劳导致轨道面或滚动体表面剥落、凹凸不平的现象。
点蚀:轨道面上产生斑点状小孔,深度约0.1 mm。


抑制光泽面的反射光,观察磨损、摩擦情况
有时候,滑动面因摩擦而产生光泽的试验片或试验球所引起的反射光过强,这会导致显微镜受光晕干扰,无法正常观察。
4K数码显微系统“VHX系列”则能够利用“消除光晕”、“去除环形光晕”功能,杜绝反射光的干扰。对于光泽度随摩擦而升高的滑动面,可抑制光晕,拍摄清晰的图像。还能分辨细微纹路划痕/摩擦痕与附着物的区别,更加正确地掌握摩擦、磨损的状态。
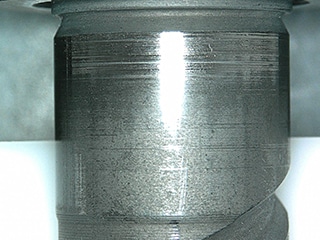

用1台设备即可进行观察和2D、3D测量
在对立体目标物进行外观观察时,必须对不同部分分别对焦,还存在漏看划痕、人为评估差异等问题。对于立体目标物,也只能通过二维尺寸测量进行评估。
4K数码显微系统“VHX系列”不仅能用清晰的4K图像进行放大观察及二维尺寸测量,还能拍摄3D形状,进行三维尺寸测量,对各个截面实施轮廓测量。不论检测人员的熟练度如何,都能通过简单操作完成3D形状的分析及测量,可同时实现摩擦部表面评估的高度化、定量化,以及作业的高效化。

快速回应市场需求的新型工具
今后,市场对摩擦磨损试验的需求会越来越大,为了顺利开展摩擦学评估,必须基于快速准确的检测数据,确立新的研究开发、品质改良模式及制造工序。
导入高精细4K数码显微系统“VHX系列”,能够实现飞跃式高效化作业,用1台设备就能实现难度很高的的高精细观察、分析、测量及评估。“VHX系列”还配备了许多其他新功能,在追求兼顾品质与速度的未来制造业,将成为非常有效的工具。
如需了解“VHX系列”的详情,欢迎点击下列按钮,下载查阅产品目录或随时咨询。