压铸件中砂眼等铸造不良的原因及测量、评估
近年来,过去多用于汽车部件的压铸件的采用范围进一步扩大。因此,铸件制造现场需要的是快速测量和定量评估,以此找出不良品及其原因,从而提高品质和成品率。
下面我们将为您介绍铸造不良的原因和对策,以及使用新型4K数码显微系统检测压铸件的应用案例。

在汽车行业适用范围进一步扩大的压铸件
将铝合金、锌合金、镁合金、铜合金等的熔融金属液压入精密模具的铸造方式或铸件叫作“压铸”。因为可以获得优异的尺寸精度、美丽光滑的铸件表面和高生产效率,所以被广泛用于各种产品。
在压铸产品的全部产量中,汽车部件占大多数。
其中铝合金压铸件比锌合金压铸件更轻且强度更高,导电性、导热性、耐腐蚀性、加工性优异,实现了成本低、循环利用性强的产品,因此多用于汽车部件。
在汽车领域中的用途,主要有气缸模块、变速箱、摇杆盖等箱壳和盖罩类。传统压铸产品大多含有气体,难以进行热处理和焊接,因此很难应用于汽车的行驶部件和车体部件等。但是,近年来通过层流压铸和高真空压铸等特殊压铸法,将其也应用到了高难度的产品中。与此同时,铸件的功能性和品质要求标准也在不断提高。
铸造不良的原因和对策
汽车部件压铸工序中需要注意的是,熔融金属和模具的温度、模具充填时的压力、金属中包含的气体或空气等造成的铸造不良。铸造不良会导致强度降低,严重关系到汽车的安全品质。
铸件的砂眼、铸件表面粗糙等内部和表面产生的代表性缺陷和不良,其原因和对策如下表所示。
铸造不良 | 原因及状态 | 对策 |
---|---|---|
砂眼 | 由于熔融金属中混入空气或气体所形成的空洞(圆形空洞、气孔)。熔融金属供给不足产生的空洞(缩孔) | 调节铸造压力,更改排气口,调整脱模剂涂抹量,更改浇口的位置和大小 |
凹陷 | 由于模具局部过热导致冷却缓慢,产生凹陷 | 调节模具温度,改良模具设计 |
填充不足(流动不够) | 距离浇口近的部分冷却较快,熔融金属无法灌注满整个模腔的状态 | 调节模具温度、熔融金属温度,更改浇口的位置和大小 |
冷隔(冷纹) | 在模具温度和浇注压力都较低的情况下,熔融金属在注满模具之前就发生凝固,在连接处产生接缝的状态 | 提高模具温度、熔融金属温度及柱塞速度,更改浇口的位置和大小 |
破裂、歪斜 | 由于拔模斜度不足、收缩不均匀、押出不恰当等原因导致。凝固过程中的破裂为高温破裂,冷却过程中或经过一定时间后的破裂为低温破裂 | 更改形状设计、押出位置 |
破断冷硬层 | 套筒中产生的凝固层被注入膜腔,被融进压铸件的状态 | 调节熔融金属温度及柱塞速度 |
熔合纹 | 在模具温度过低或脱模剂用量过多时发生 | 提高模具温度,减少脱模剂用量 |
拉模 | 取出压铸件时,铸件熔敷在模具上或拔模斜度不恰当时产生刮伤 | 充分研磨模具表面,设置合适的拔模斜度 |
粘模 | 由于模具局部过热,导致模具与熔融金属发生熔敷的状态 | 更改脱模剂的种类及涂抹方法,改良模具设计 |
气泡 | 接近表面的压缩气体膨胀,使铸件表面出现鼓起的状态 | 采取与砂眼同样的对策以及延长模具冷却时间 |
变色 | 由于脱模剂的成分导致压铸件表面变色的状态 | 更换脱模剂 |
表面粗糙 | 因模具表面的粗糙度被直接压印到压铸件表面而发生 | 清理、研磨模具 |
硬点 | 金属溶液内混入坚硬异物时发生。可能会在后段工序中导致研磨工具等破损 | 对金属溶液进行过滤处理 |
除上述之外,还有各种原因会导致铸造不良。对于压铸件的品质保障来说,品质检测至关重要。微小的孔穴、空洞、表面粗糙度不良等关乎品质,因此需要高精度的分析、测量和评估。
压铸产品检测的应用案例
通过显微镜放大观察,是对砂眼和铸件表面进行评估及不良分析不可或缺的项目之一。但是,压铸产品是立体的,所以存在对焦的人力、观察及分析的难易度、不良评估的误差等课题。
因此,借助数码显微系统的放大观察持续增多。凝聚新技术的基恩士超高精细4K数码显微系统“VHX系列”,在清晰捕捉压铸件砂眼和表面并进行定量化评估的同时,成功地大幅提高了作业效率。
即使提高倍率也能持续全幅对焦的变焦拍摄
部分显微镜在根据目标物大小和分析位置更换镜头时,会因改变倍率、对焦而花费人力和时间。
4K数码显微系统“VHX系列”配备了高分辨率“HR镜头”和“电动镜头转换器”,无需更换镜头就能进行20至6000倍的自动倍率切换,实现“无缝缩放”。只需用手边的鼠标或控制器进行直观的操作,1台设备就能快速完成全套操作,除了通过基于深度合成对工件整体全幅对焦的高分辨率图像进行观察之外,还能通过自动面积测量和3D形状、轮廓测量进行定量评估。


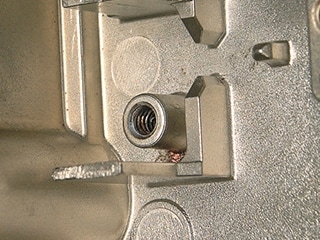


通过简单的操作实现自动面积测量(左下)和3D形状、轮廓测量(右下)。
砂眼的3D形状、轮廓测量
4K数码显微系统“VHX系列”可以根据高度信息来测量3D形状和轮廓(二维截面形状)。凹凸不平的压铸件表面也以全幅对焦3D显示,砂眼、气孔等表面形状的细微变化也不放过。
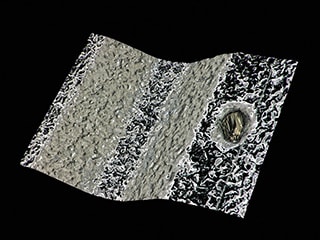

细微砂眼的高倍率图像
过去用于观察砂眼的显微镜存在倍率和分辨率不足、无法对焦等课题。
4K数码显微系统“VHX系列”则对于细微砂眼也能高倍率清晰拍摄。
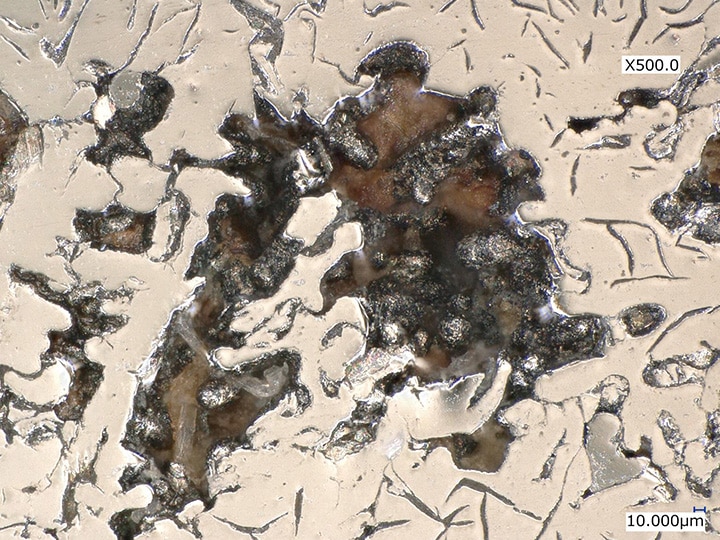
压铸模具的手持观察
铸造不良不仅源于熔融金属的温度和压力,也有不少是因为模具的状态。特别是铸件表面粗糙等不良,大多是由于模具内部的细微外观不良造成的,所以模具的检测也必不可缺。
但是,汽车部件的铸件模具大多是大型模具,不可能切割后再用显微镜进行观察和分析。而在部分手持显微系统的非破坏性检测中,存在对细微裂纹分辨率不足的课题。
4K数码显微系统“VHX系列”即使在使用手持镜头时,也可通过4K图像放大观察模具上的细微裂纹等不良部位。

压铸模具裂纹的3D形状、轮廓测量
4K数码显微系统“VHX系列”实现了3D形状、轮廓测量。在通过高倍率图像实现直接高效定量检测的同时,还可以使用不同镜头,应对模具、小样本等多种分析检测用途。


铸件表面的自动面积测量和定量评估
4K数码显微系统“VHX系列”在立体铸件表面的二维检测方面也是强有力的工具。借助自动面积测量、计数功能,能够以简单的操作对铸件表面的不良部位进行定量评估。
这样不仅可以在不放过表面粗糙等不良的情况下进行定量评估,还可以利用报告功能瞬间制作使用图像和数值数据的报告。除了仅用1台设备即可完成一系列的作业之外,还能大幅缩短作业时间。


用1台设备就能改变压铸现场
高精细4K数码显微系统“VHX系列”不仅可以通过高分辨率4K图像进行清晰的放大观察,还能以1台设备进行自动测量和2D/3D测量,因此可以快速进行定量评估。
“VHX系列”可以迅速获得在压铸现场出现的砂眼和铸件表面粗糙等问题的详细图像和数值,有助于快速确定不良原因并防止不良复发。因此,在扩大压铸产品用途和提高功能要求方面,它都是提高品质和成品率不可或缺的1台设备。
如需了解“VHX系列”的详情,欢迎点击下列按钮,下载查阅产品目录或随时咨询。